Haydon Bridge Construction offers Design-Build services, which is a mode of procurement that we utilize to provide each project with the best value regarding process, materials and skilled labor, rather than making decisions solely based on cost. Design-Build is defined as a method of project delivery in which one team works under a single contract with the project owner/manager, to provide design, planning and bridge/road construction services. The benefit? Design-Build services streamline project delivery through a single contract between the project owner/manager and the design-build team.
What is Design-Build?
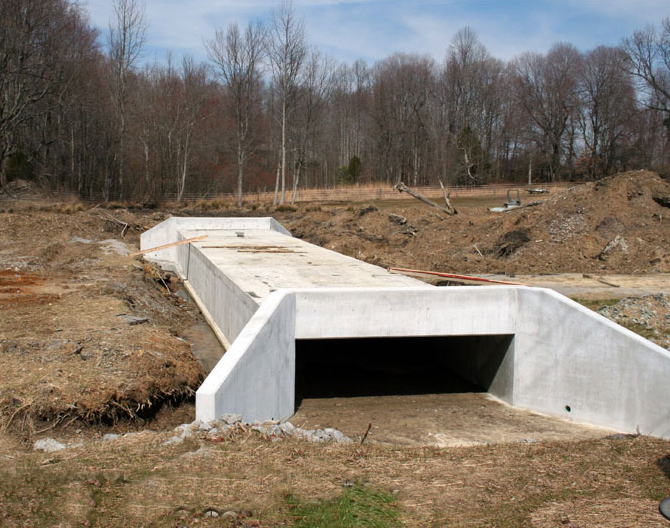
What is the Process for Design-Build?
In the Design-Build service, there are various steps from project procurement to project completion:
- MEETING: The management team will schedule a meeting with the project owners and managers to determine and review project expectations.
- PLANNING: After full review of timeline, resources, budget, project goals, the engineering team meets to develop accurate and detailed plans.
- RFP: A Request for Proposal is issued, also known as the procurement process. The Design and Build procurement includes the process of securing bids with a focus on timeliness, acceptable quality, financial parameters, minimizing and mitigating risk, effective communication and administration, and most importantly, ensuring clients’ satisfaction by fully understanding the project objectives.
- SELECTION PROCESS: The owner then shortlists up to three bids, with a full consideration of each teams’ technical proposal and price proposal. Each project owner has an individualized scoring system based on price, quality and timeline. Each RFP will be weighed on these scoring parameters and then a final choice is made. Once chosen, a public announcement will be issued of the chosen design-build team who was awarded the contract.
- KICK-OFF MEETING: The awarded contract team’s partners and engineers will meet internally to discuss and review all project plans. After which a meeting with the project owner and managers is scheduled to go over any changes and review all project expectations.
- SCHEDULE DETERMINED: After all the above meetings, a project schedule is set into builder units, for each portion of the project, enabling the project to begin construction before the entire project plan schedule is finalized and approved.
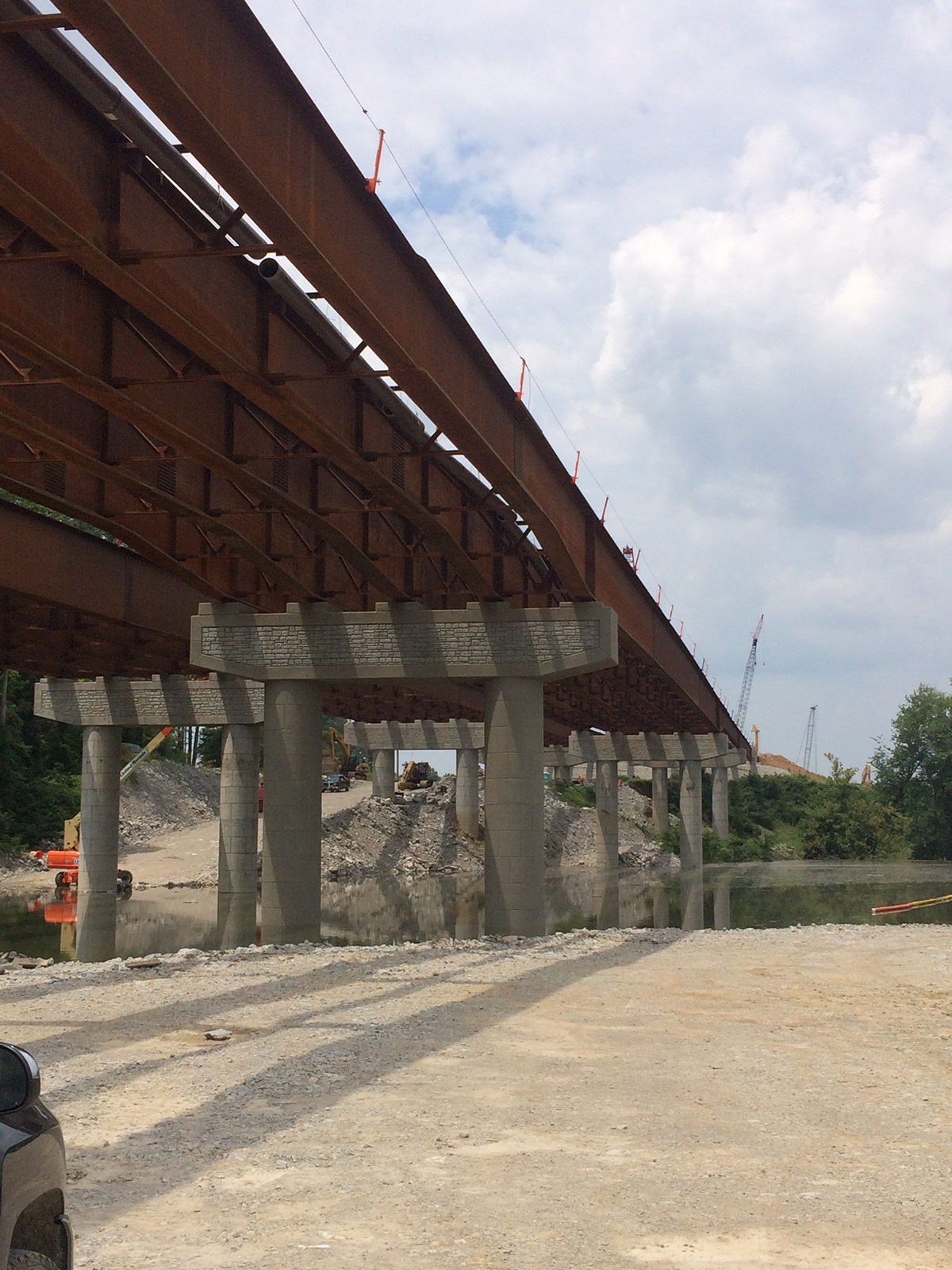
What is the Timeline for Design-Build?
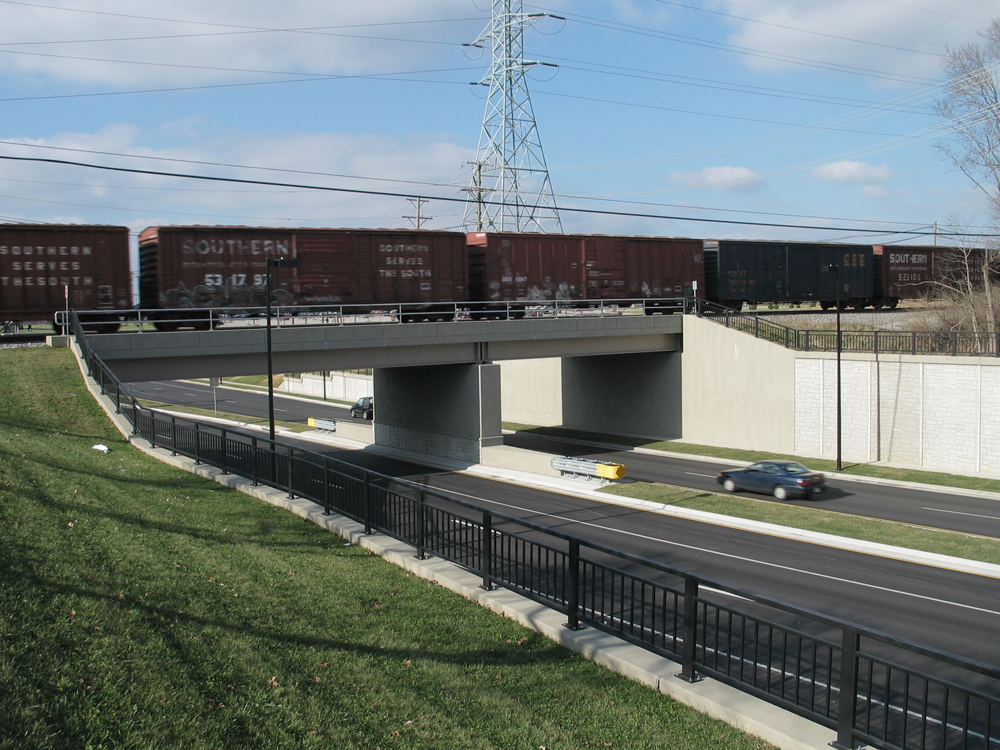
A fully developed plan using traditional Bid-Build may take years to finalize, so instead of delaying the progress of the work, we can work on both items simultaneously, when the project is broken down into buildable units. For example, once a design-build contract is initiated and approved, the project team begins working on designing and constructing the project in buildable units, which allows construction to begin prior to final design of the entire project. This concurrent activity of design and construction takes extensive coordination between the designers and contractors; however it significantly speeds up the project delivery to the public.
Why Choose Haydon Bridge Company for Design-Build?
- Competitive Quote: After a full review of the RFP and meeting with the responsible parties, we review the scope of the project, the estimate timeline from start to completion, determine cost of materials, labor and subcontractors, review potential obstacles in projected construction site; and submit a comprehensive design/build proposal. Our team has the experience, resources and expertise to meet the project goals while minimizing cost.
- Our Responsive Project Team: We work closely with the project manager/owner, the subcontractors, the suppliers, the engineering team to provide an organized and communicative delivery of services. Before we begin each project, we ensure we employ the skillsets and expertise of our team members and engineers who are best suited to the specific project, as well as qualified subcontractors. Our Haydon Bridge staff project manager has direct contact to the design-build team and all project parties. Therefore, if an issue or challenge arises, we have the ability to quickly and efficiently resolve the issue with an expedited timeline. We can also quickly communicate with both owner and engineer, which are employed by the contractor, so all parties are kept updated of project status, progress and any required changes in the original plan.
- Application of Design Specifications: Once the project owner/manager provides the final approved design specifications, we work to implement their specs effectively, accurately, and in great detail to meet the owner’s desired outcome, within their means and methods agreed upon (timeline, resources, equipment, personnel, skillsets, and budget). As Haydon Bridge utilizes state-of-the-art equipment, software, technical resources, and our full team of skilled engineers, we are one of the most competitive Kentucky companies in the bridge construction industry.
- Focus on Quality Work: Our commitment to the most efficient design with state-of-the-art equipment and process, we are able to respond to challenges while also meeting the deadline schedule.
- Innovative Solutions: Using the Design/Build procurement method, we have been involved in multiple projects that required innovative solutions to meet the project goals. Some of these solutions include Lateral Sliding of Bridges, Post Tensioning, intricate Earth Retention Systems, Prefabricated Lightweight Structures, etc. We pride ourselves on utilizing Innovative Solutions to solve project issues while meeting or exceeding the project goals.
- Experience: Haydon Bridge has been a leader in the design/build market in the Commonwealth of Kentucky. With over 50 years in the industry, we have well established relationships with Design Engineers, Specialty Contractors, etc.
- Collaborative as a Subcontractor: When Haydon Bridge is not the lead contractor, but serving the project as a subcontractor team member, we are dedicated the project objectives and we treat the project no differently than if we were the prime contractor. We go through all the same processes and provide the same quality work and collaboration regardless of our role in the project.
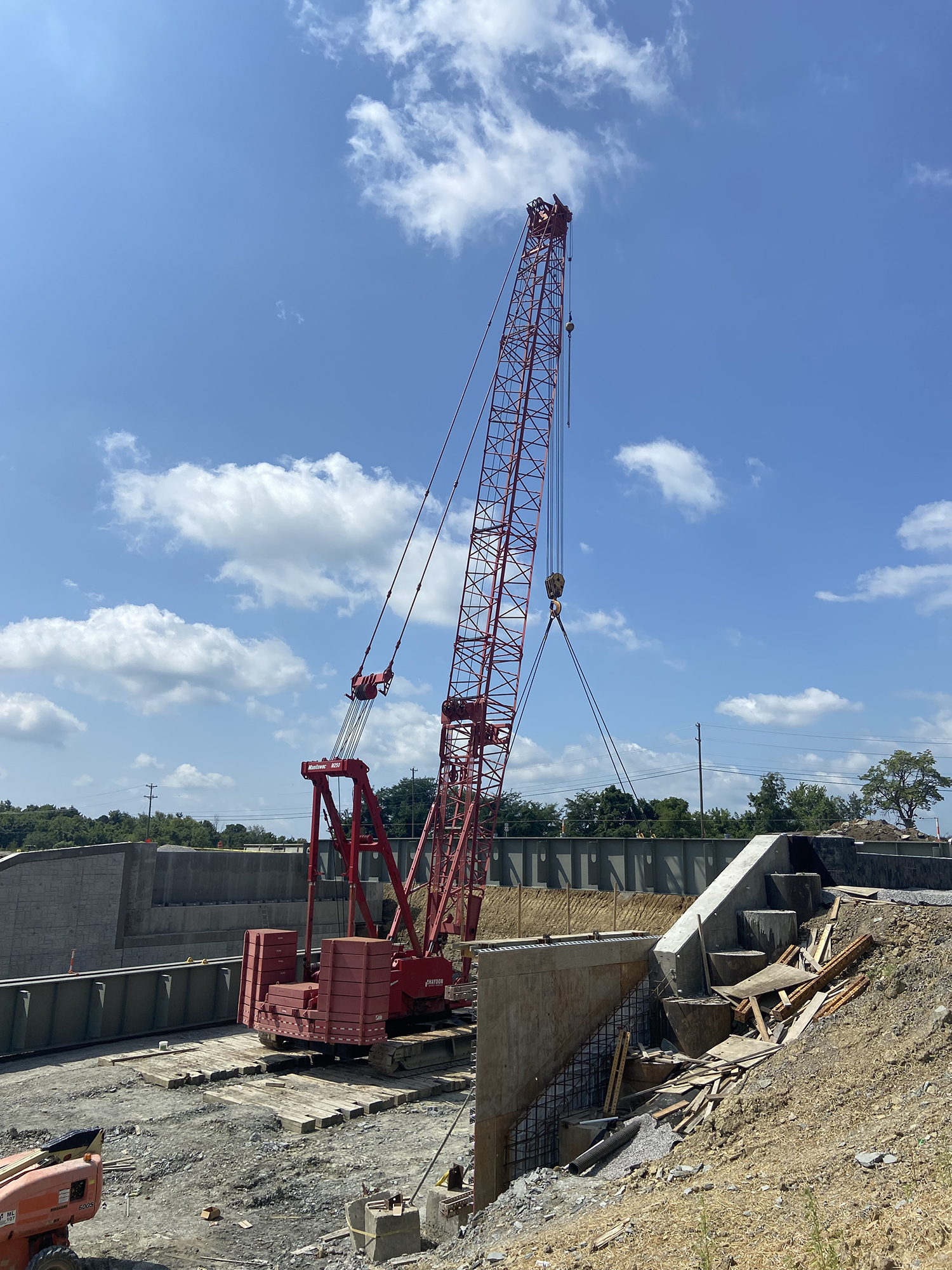
CASE STUDY of Design-Build Project
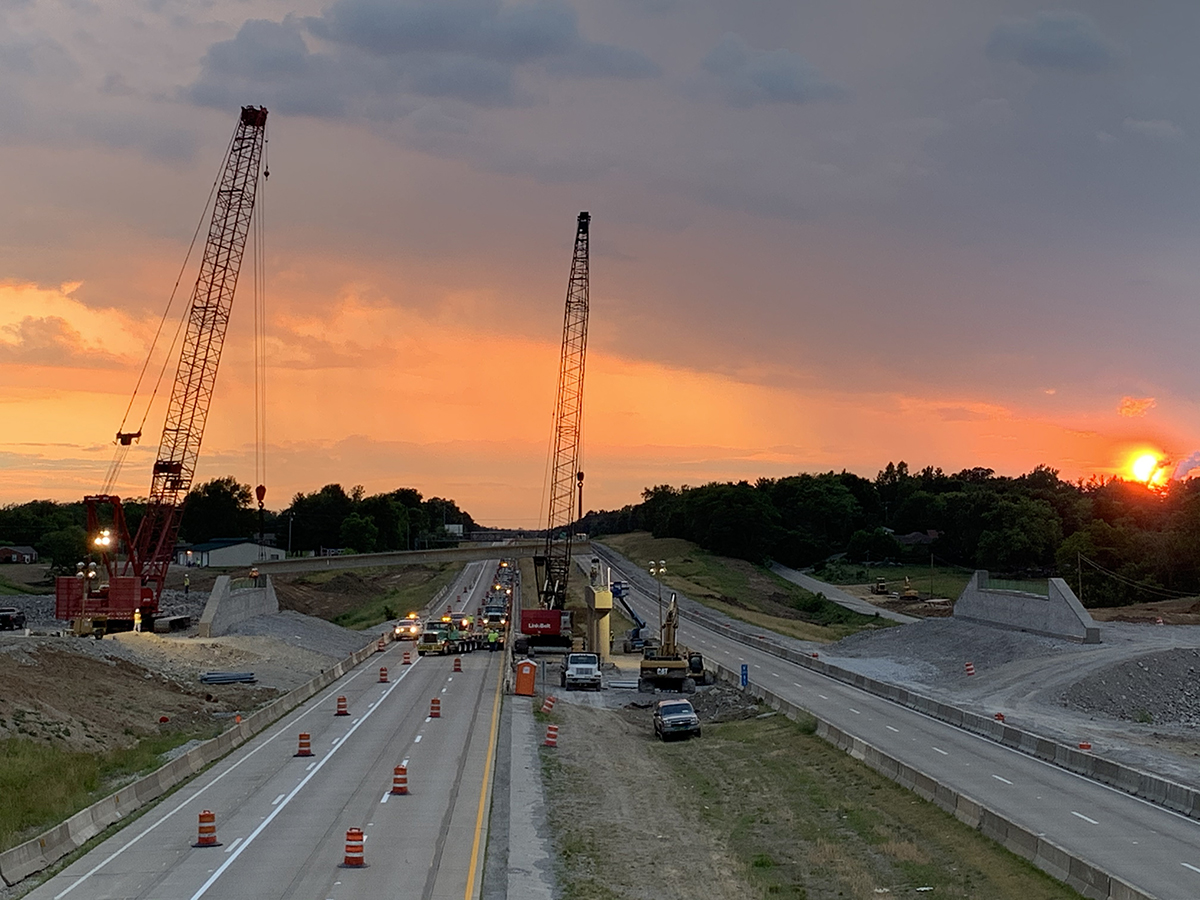
On the Boone County – Graves Road project, Eaton Asphalt Paving Company was the prime contractor while Haydon Bridge Company served as subcontractor on the structural portion of the job, including:
- Bridge on Graves Road over I-275
- 3 Reinforced Concrete Box Culverts
- 1 Retaining wall
We cooperated and shared intellectual and physical resources with the other contractors, providing value to the overall success of the construction. We were able to add value outside of just the structural work going above and beyond by providing the prime contractor with consultation and expert advice from our 50 years’ of experience.