Haydon Bridge Company is Kentucky’s premier bridge contractor for more than 50 years, with our family-owned company now spanning three generations. So, there is no question that we are experts on bridge construction, repair and rebuild. We work closely with engineers and our safety manager to ensure all parts of the construction process is reliable, safe and completed to ensure durability and quality of each bridge, roadway, or overpass we construct. We are proud of our work and it shows.
An essential and important step of the process of bridge construction includes the steel erection of the bridge’s truss, girders, beams, and/or temporary support columns.
WHAT IS STEEL ERECTION?
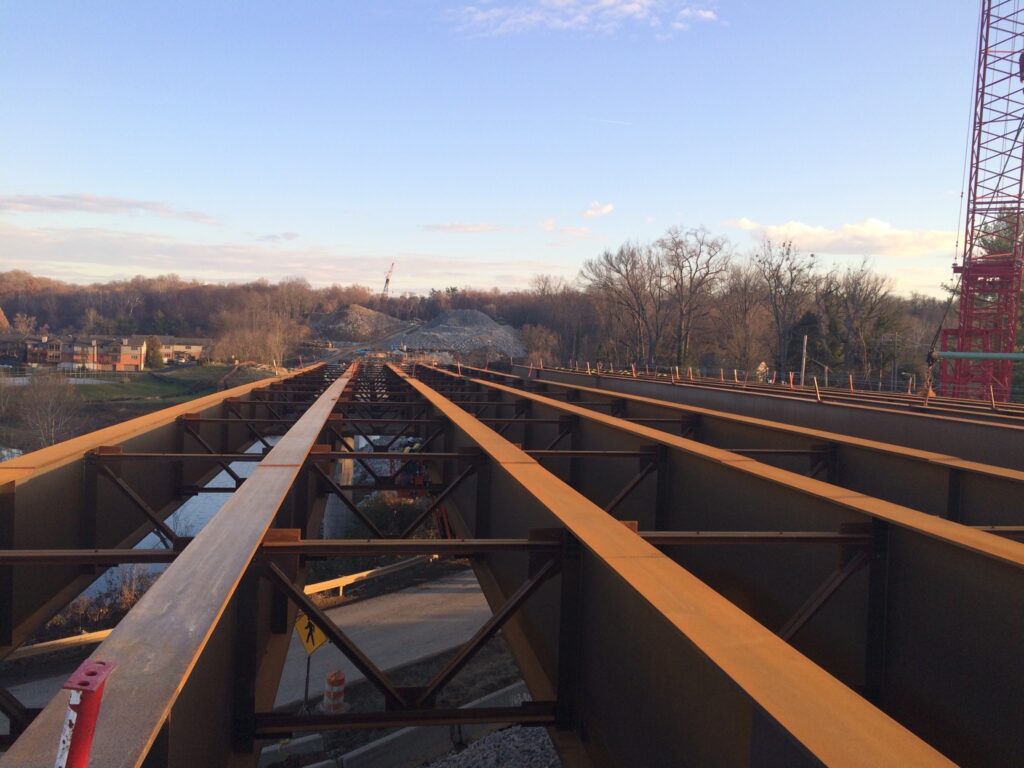
Steel erection is the process of constructing, altering, or repairing bridges and overpasses, and it involves the assembly, connection, and installation of steel beams, metal decking, and planking used in the erection of the bridge structure. For bridges particularly, it’s erecting the steel plate girders or trusses that support the bridge, splicing (or bolting them together) when lifted in the air or on the ground, then erecting them and putting the structures into place.
Simply put, steel erection in bridge construction involves the assembly and installation of structural steel components to create the framework of the bridge superstructure. We take this phase of bridge construction very seriously as it is a critical phase of bridge construction which requires careful planning, skilled labor, and strict adherence to safety and quality standards.
WHAT TYPES OF GIRDERS ARE ERECTED ON BRIDGE CONSTRUCTION?
Determined by the engineers in the planning and design phase, we can use various types of girders on bridge and highway construction, which is determined by an analysis of each girder’s advantages and limitations. Factors determining the type of girder used are span length, load requirements, site conditions and even aesthetic considerations.
Here are some of the girder or truss types we commonly use:
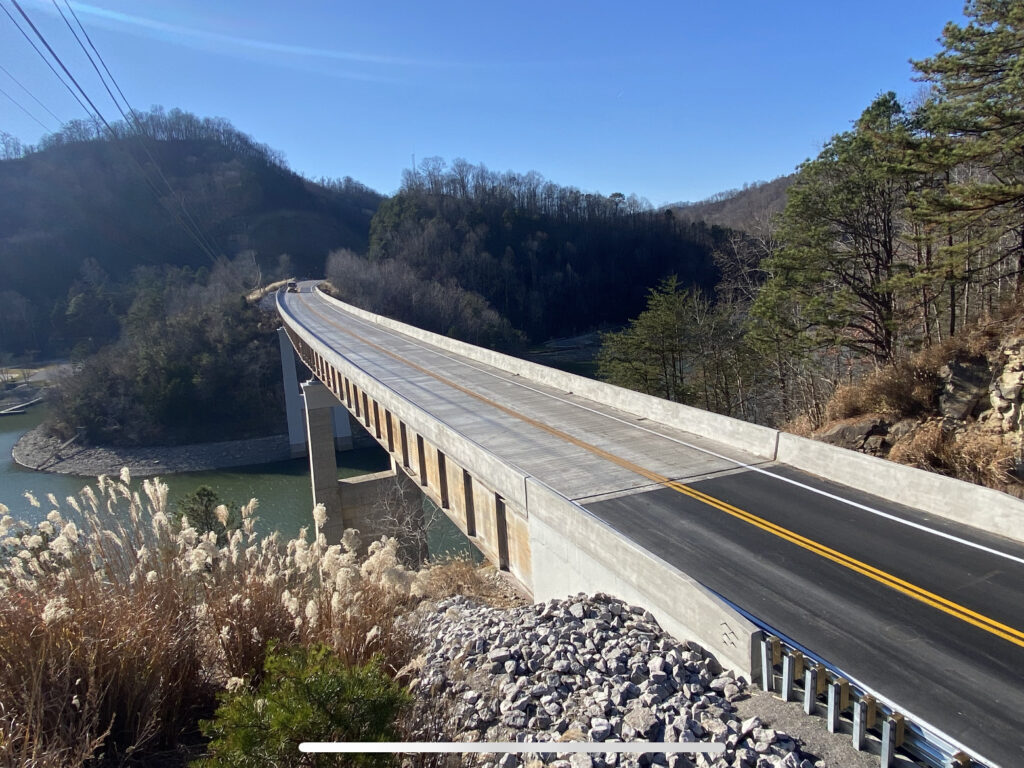
- I-Beams: I-beams, (also known as rolled steel joists RSJs or universal beams UBs) have a cross-sectional shape resembling the letter “I” and are efficient in resisting bending forces.
- Box Girders: Box girders consist of a closed rectangular or trapezoidal cross-section, resembling a box. Box girders can be made of steel, concrete, or composite materials.
- Plate Girders: Plate girders are made by welding together steel plates to form a beam-like structure.
- Trapezoidal Girders: Trapezoidal girders have a cross-sectional shape resembling a trapezoid, with a wider top flange and narrower bottom flange.
- T-Beams: T-beams have a cross-sectional shape resembling the letter “T”, with a wide top flange and a narrower stem. T-beams can be made of steel, concrete, or composite materials and are often used in highway and railway bridges.
- Composite Girders: Composite girders consist of a combination of steel and concrete elements, with the concrete typically encasing the steel section.
- Cable-Stayed Girders: In cable-stayed bridges, the main girders are supported by cables anchored to tall pylons or towers.
- Truss Girders: Truss girders consist of a framework of interconnected steel members arranged in a triangular pattern.
WHAT ARE THE STEPS FOR STEEL ERECTION?
The process of erecting the steel structures including the following steps:
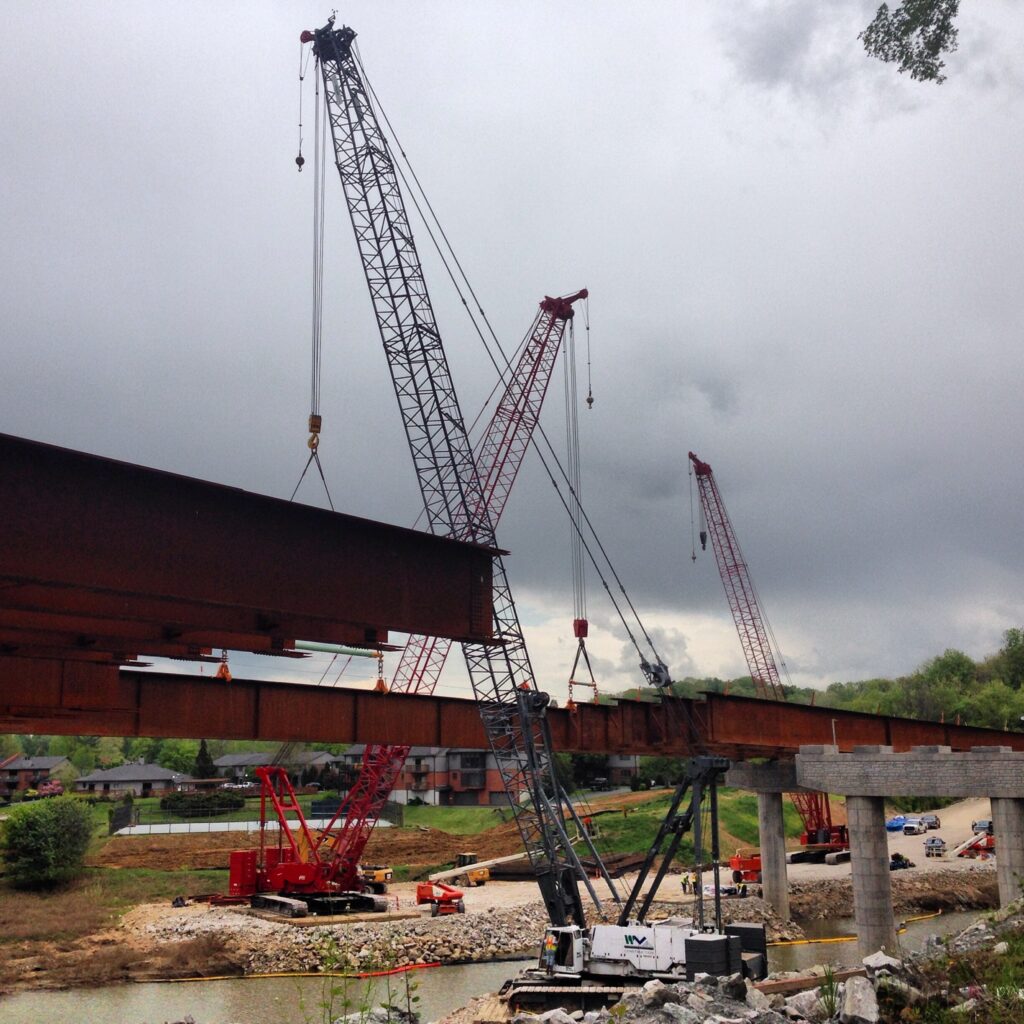
- PLANNING. The first step of any construction project is the planning and build-design phase which is conducted by our team of skilled bridge and highway engineers. Our team of skilled and experienced engineers consider various factors including intended use of the bridge, roadway or overpass, site conditions, nearby waterways with their corresponding flood zones, intended load and performance requirements, environmental factors, and regulatory requirements.
- PREPPING THE JOB SITE. Preparing the job site for erection of the steel superstructure and structures, which could involve setting up temporary support structures, and ensuring that safety measures are in place.
- FABRICATION. Structural steel beams, girders, trusses or columns are often fabricated either offsite or for transportation limitations, on site. The fabrication involves cutting, welding, and bolting/splicing the steel to the required dimensions and configurations for the bridge span length and width.
- ON SITE FABRICATION IF NEEDED. If fully or partially constructed off site, the steel structures are transported to the job site, and if need be, if too long or too large to transport, the completion of splicing will happen on the job site.
- PREPPING THE PIER CAP. Prepping the girder of the pier cap or substruction to allow for safe and secure placement of the beams, girders, trusses or steel columns. Temporary shoring towers may be needed to hold the girders in the air until the next steel structure arrives. The steel girder may sit on bearing pads and is bolted to the previous girder with splice plates and using cross frames to hold each component together side by side.
- LIFTING THE STEEL ERECTION. Cranes are used to lift and place the steel structures into place, with careful planning, precision and positioning. This process requires precise coordination and alignment to ensure the structural integrity of the bridge. The cranes lift capacity is a huge factor that is considered before each critical lift of the truss or beam. If the crane’s capacity is exceeded by 75% of the weight radiance, we will use two cranes to compensate for the additional weight.
- SPLICING THE ERECTIONS. Now it’s time to connect the different girder segments together using high strength bolts (also called splicing), and splice plates to ensure a secure connection along the girder line.
- WELDING, IF NEEDED. Once in place, we ensure that the structure is securely connected to the substructure using welding. Our skilled welders carefully weld the joints according to the engineers’ specifications to create strong, durable joints.
- QUALITY CONTROL & TESTING. After the steel erections are in place and the framework of the bridge is in place, our team conducts quality controls and safety testing to ensure the work meets engineering standards and specifications. This may include inspections of the welding, bolted connections, and overall structural integrity.
- COMPLETION OF BRIDGE CONSTRUCTION. Once tested, the next phase of bridge construction can resume which may include the installation of decking, railings, and other finishing elements.
SAFETY CONSIDERATIONS IN STEEL ERECTION
When erecting steel structures, we understand the substantial damage and safety risk to the bridge’s framework, the construction workers and subcontractors, and nearby properties/roadways. First and foremost, we are focused on the health and safety of our employees and any persons near or on the job site. Our safety manager works together with the team to ensure all safety risks are assessed for proper handling, procedures, and prevention of accidents, before any construction, lifting or erection begins.
Our employees are regularly trained as well as provided detailed safety procedures specific to each project. They are instructed on how they must adhere to our strict safety protocols including the use of personal protective equipment (PPE), fall protection systems, and proper rigging techniques, as well as crane operations. Our safety manager is involved through all stages of steel erection from the planning to completion and cleanup of the job site, with periodical visits to conduct assessments that all safety procedures are being followed.
CASE STUDY: PULASKI COUNTY, KY PROJECT
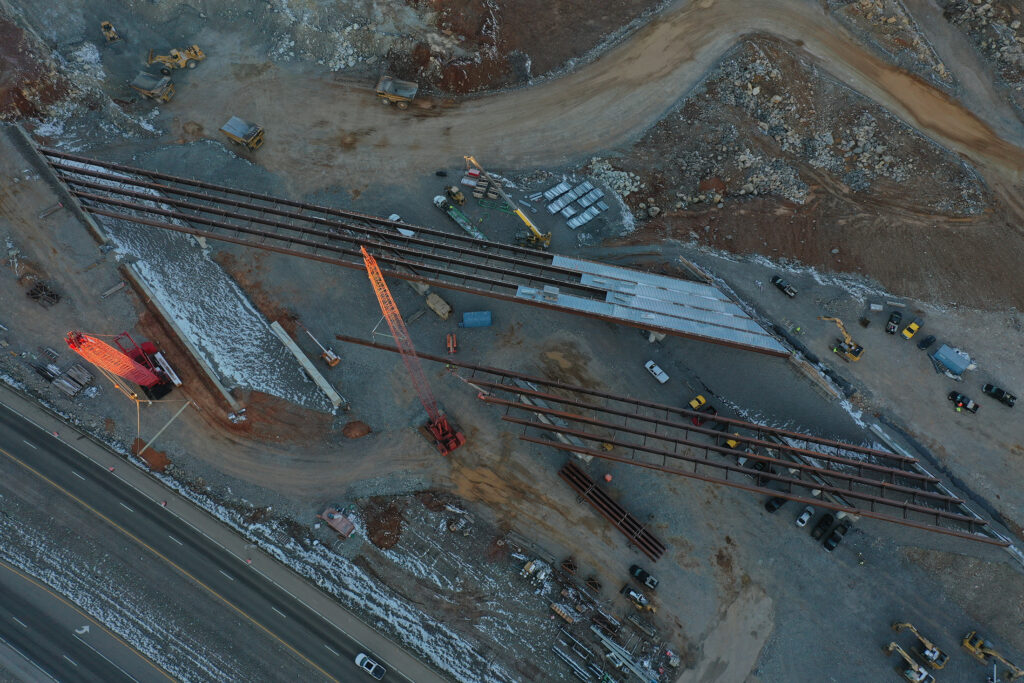
Shows a Manitowoc 777 crane erecting the outside girder line to previously erected girders while iron workers are in the man basket bolting the spliced connection together. Also shown on the other bridge the start of SIP (Stay-In-Place Form) installation between the girders.
Shows a Manitowoc 777 crane holding a girder in place waiting for the next section of steel girder to be swung in and connected thru a splice across the pier cap and end bent. While a Manitowoc 2250 is unloading girders in the background and girders being delivered.
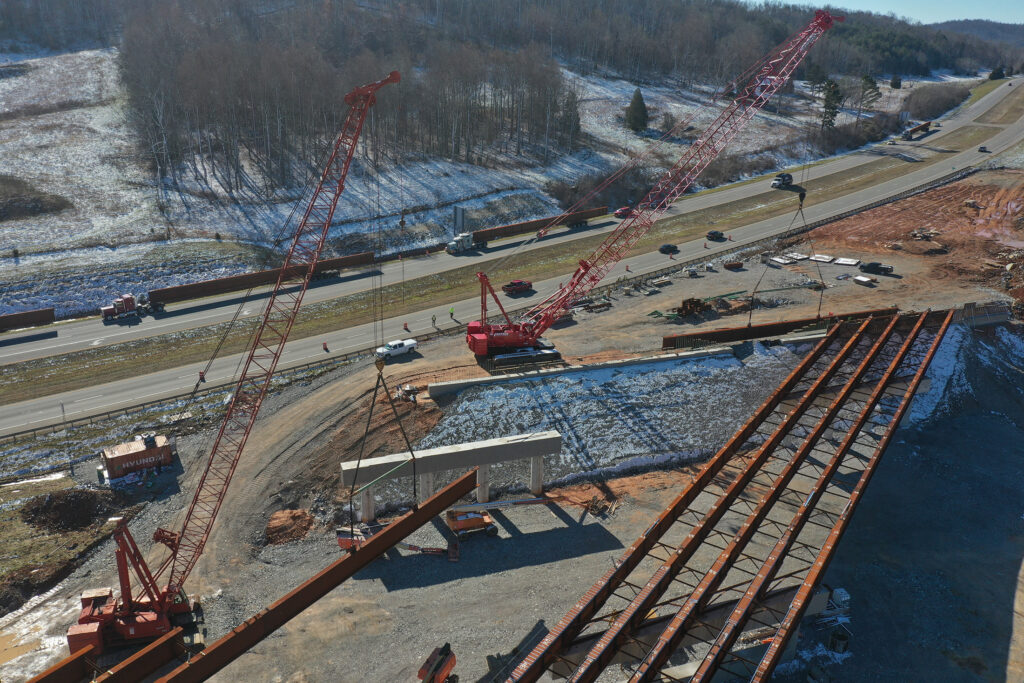
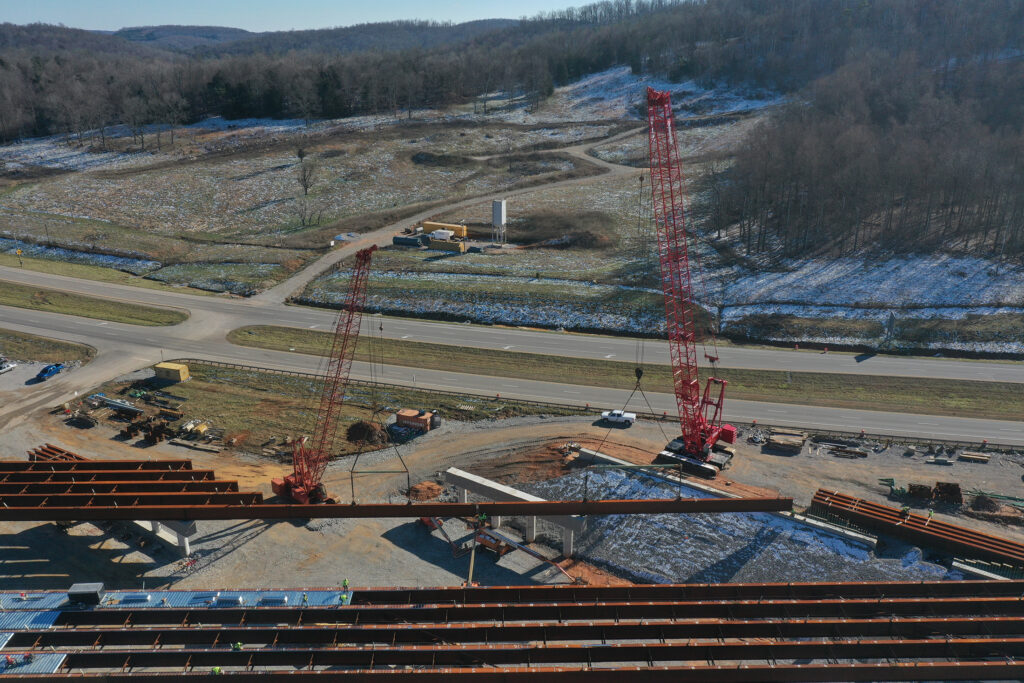
Shows a Manitowoc 777 crane holding one section of girder and a Manitowoc 2250 swinging in the next section across the pier cap and end bent while iron workers in a man basket bolt the connected splice together with splice plates and bolts.
CASE STUDY: HARRODS CREEK, KY PROJECT
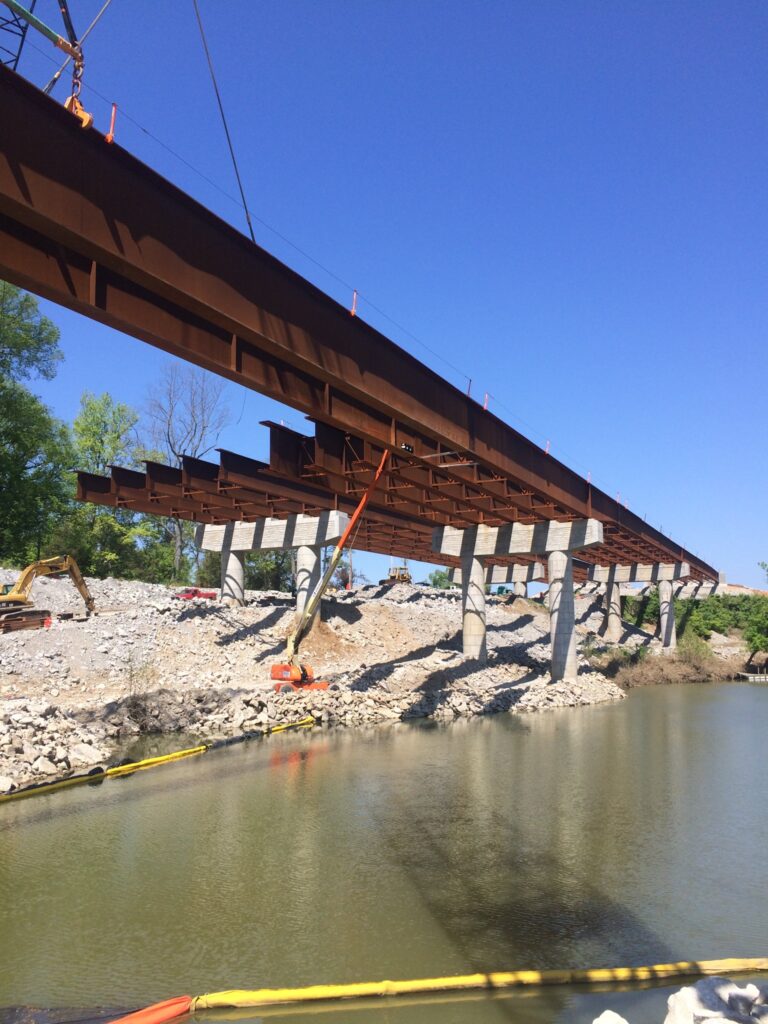
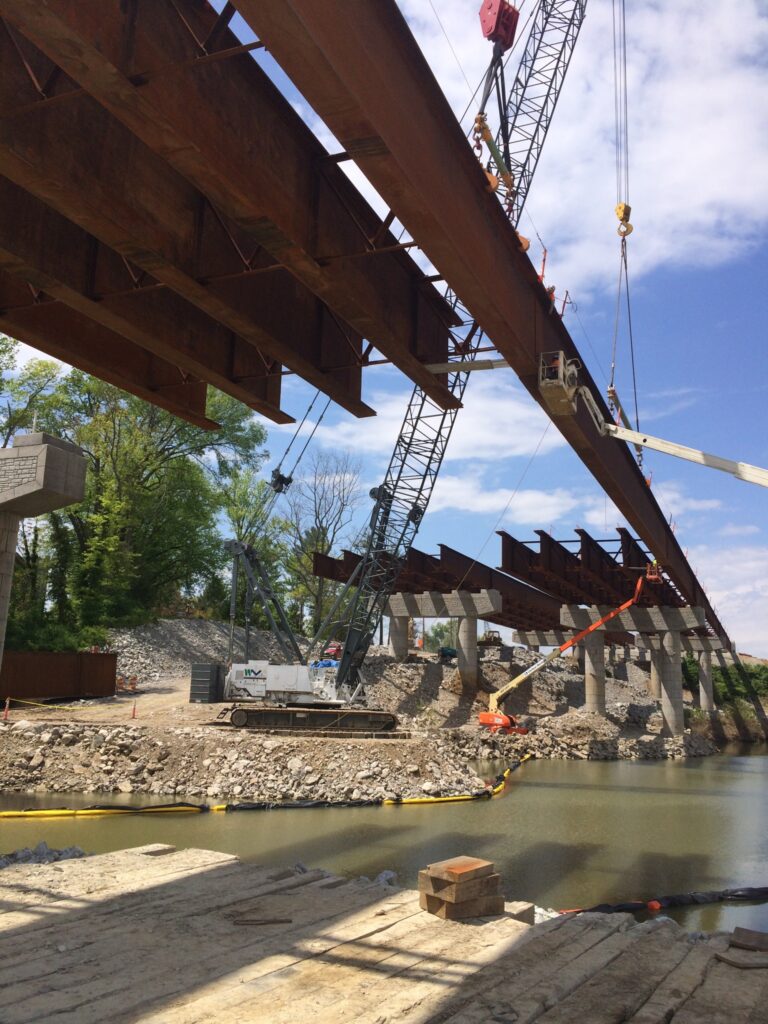
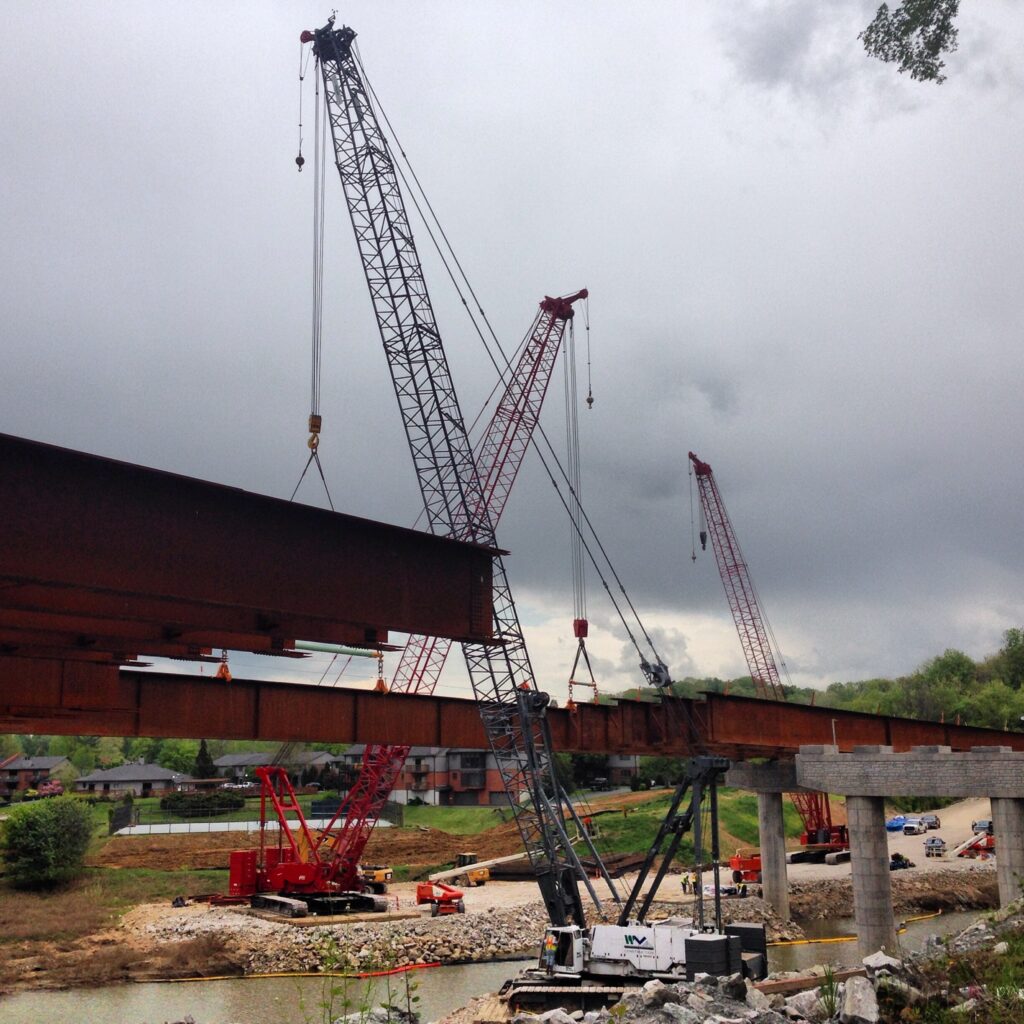
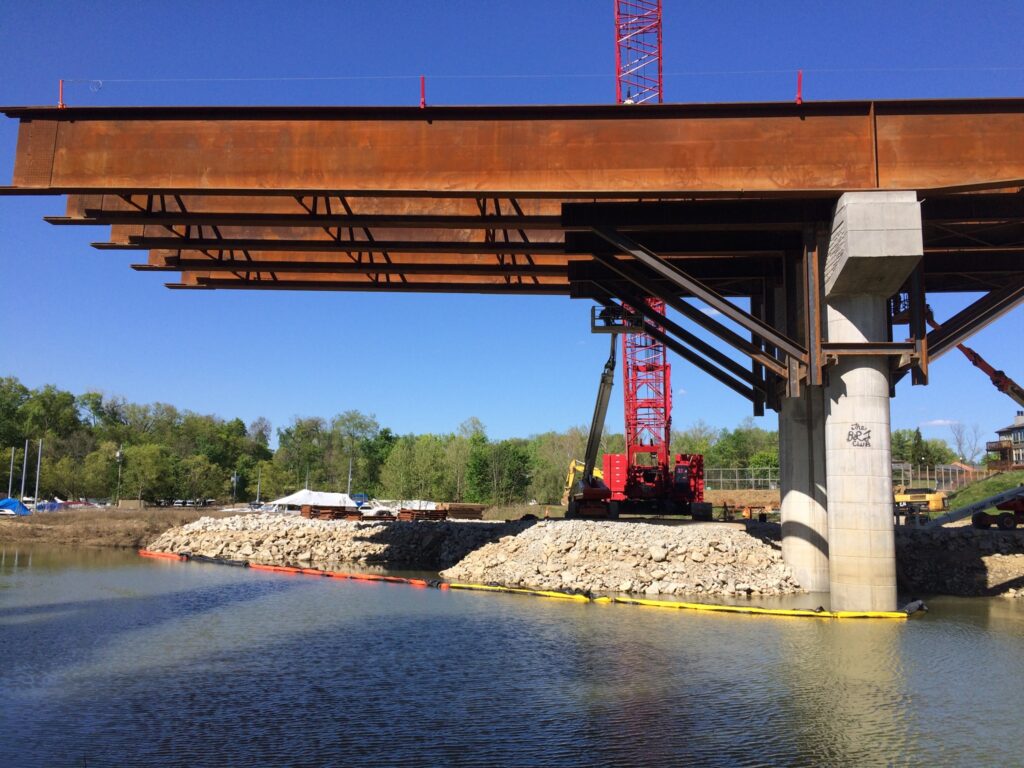
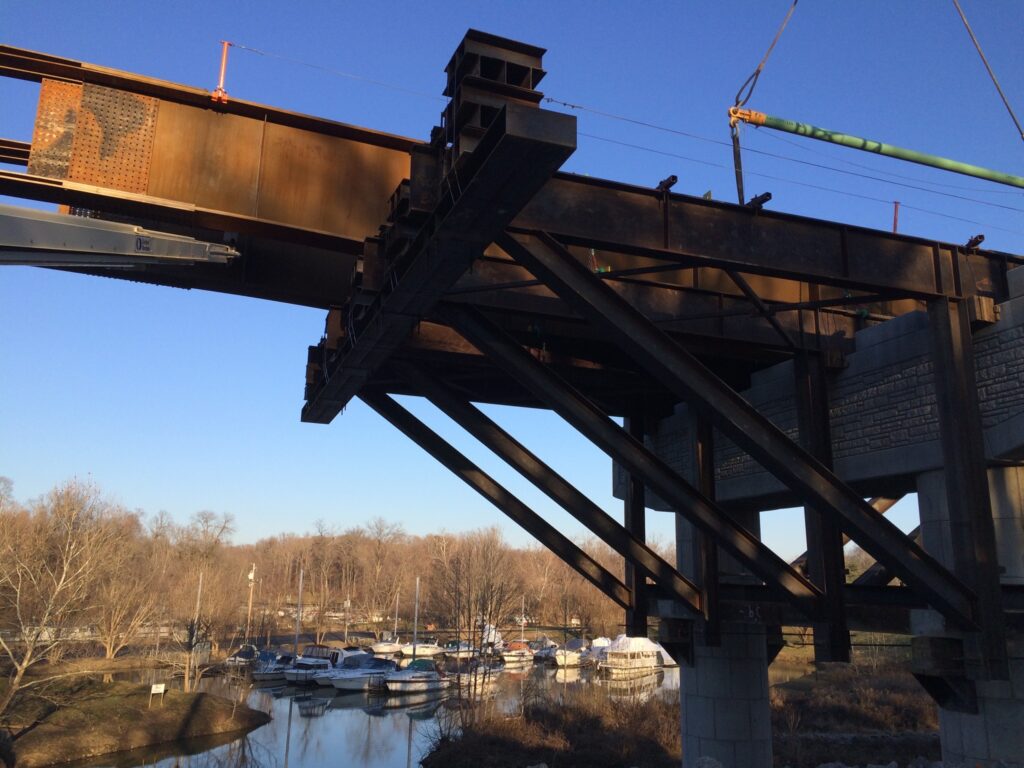
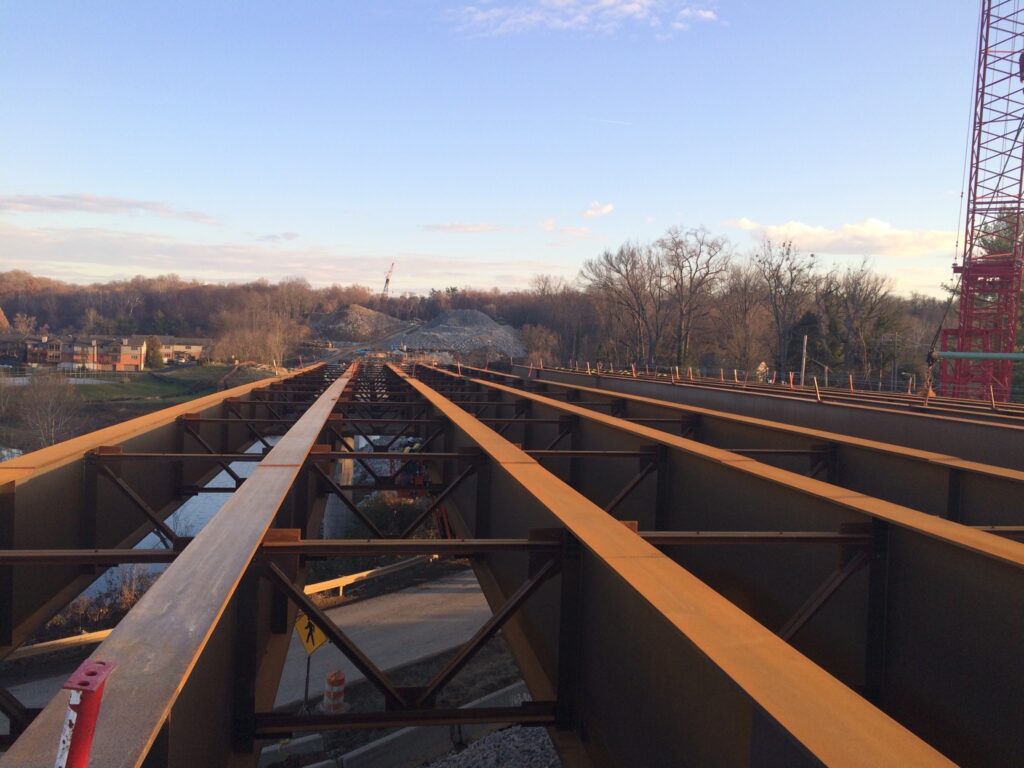