Job Statistics:
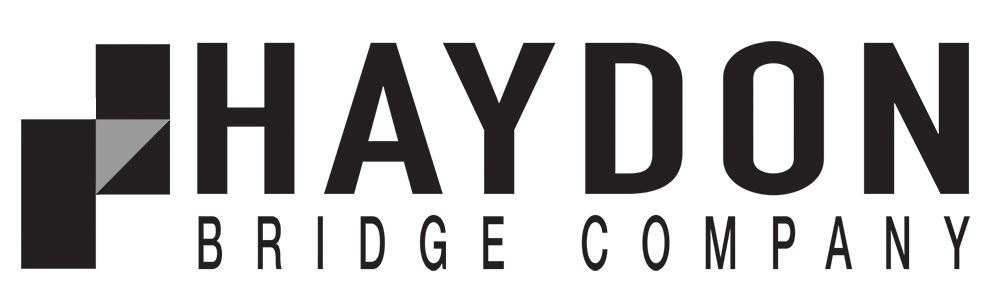
- Bid date: August 2019
- Prime Contractor: Hi-View, LLC
- Owner: Kentucky Transportation Cabinet
- Our Role: Major Subcontractor in the construction of three bridges and 6 reinforced concrete box culverts.
- Start date: Haydon bridge Start date was (November 20th, 2019)
- Completed date: Haydon Bridge Completion Date (June 7th, 2024) – The Project is still underway with the Prime Contractor, Hi-View, LLC, continues working toward the completion, by early 2025.
- Project Objective: This project was up for bid to continue and expand on the previous Mountain Parkway Expansion Projects.
Case Study Questions & Answers
What was the role of Haydon Bridge Company on this project? And why was Haydon Bridge chosen as a good fit for this job?
The KYTC awarded the project to Hi-View LLC because of their competitive bid with Haydon Bridge Company, and on this project we were in the role of a Subcontractor to Hi-View LLC. The project was in its early stages when Haydon Bridge Company was awarded the contract. Soon after Hi-View LLC was awarded the main job, the subcontract with HBC was signed, positioning HBC to begin work promptly and integrate smoothly into the project’s initial phases. For this project, we provided heavy civil concrete construction services for all the major structures involved. Our expertise ensured that each element was built to the highest standards, contributing to the overall success of the project.
Haydon Bridge was an ideal choice for the job due to their experience and expertise, their commitment to quality, and their ability to effectively collaborate with the prime contractor, subcontractors, and the Kentucky Transportation Cabinet (KYTC). Their extensive background and proficiency ensured that they understood the technical requirements and challenges of the project, while their dedication to maintaining high standards guaranteed quality results. Additionally, Haydon Bridge’s effective communication and teamwork with all project stakeholders facilitated smooth coordination and contributed to the project’s success.
Who were the major subcontractors and major material suppliers?
Major Subcontractors:
- Hayes Drilling – Drilled Shafts
- Bar-Tie Reinforcing – Furnish and Install Steel Reinforcing and Install SIP forms
- Geotechnology, Inc. – Rock soundings and corings
Major Material Suppliers:
- Prestress Services, Lexington, KY – Prestressed Concrete Beams
- Wells Ready Mix – Ready Mixed Concrete
- CMC Steel – Steel Reinforcing
- Skyline Steel – H Piling
- Bottoms Engineering and Services – Miscellaneous metals
At which stage did the listed subcontractors and the prime contractor provide their services?
- Subcontractor Bar Tie was responsible for tying all the reinforcement throughout the project.
- Geotechnology completed the core drilling at both Johnson Creek and Cutino Road.
- Subcontractor Hayes Drilling was brought in to complete the drilled shafts at Johnson Creek and Cutino Road, as well as the pre-drilling at the Johnson Creek end bent 2.
- Innovative Demolition handled the demolition of the existing bridge on Cutino Road and the bridge over the old Mountain Parkway. Additionally, a change order was approved for the demolition of the old bridges over Johnson Creek and KY 134.
What was Haydon Bridge Company assigned tasks including size of each bridge/culvert and location?
All the structures of the expansion project was located in Magoffin County. This segment of the Parkway runs from just west of the Cutino-Hager Road overpass to just west of the Middle Fork of the Licking River Bridge. It covers 4.6 miles, from mile points 65 to 69.6.
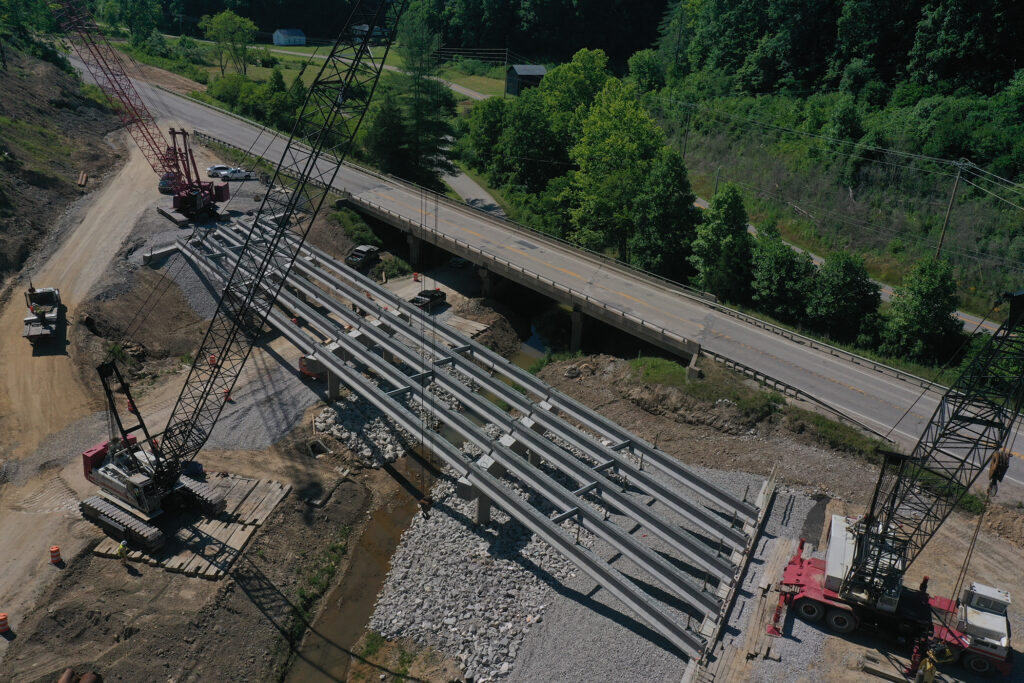
Six Culverts Constructed:
- 4 each of 4’x6’ Box Culverts Ranging in length from 712’ to 1269ft long – November 2019 to December 2020
- 1 each of 16’x8’ Double Barrel Culvert, 540ft long and over 5,600CY of Concrete – October 2021 to June 2022
- 1 each of 8’x6’ Box Culvert 150ft long – November 2023 to December 2023
Three Bridges Constructed:
- Twin Bridges over Cutino Road 243ft long (4 Span Bridge) – For Cutino Road Eastbound: Substructure began August 2021 and Superstructure Completed September 2022. For the Cutino Road Westbound: March 2023 to August 2023
- Twin Bridges Over Johnson Creek 383ft long (4 Span Bridge) – January 2021 to July 2022
- Twin Bridges Over Cow Creek Rd. 155ft long (3 Span Bridge) – Substructure began January 2023 Completed June 2024
How large was the crew assigned to this project?
The crew sizes varied throughout the construction process, but the typical crew composition included the following:
- For the 4×6 and 8×6 culvert crews, the team consisted of a foreman, an operator, a carpenter, and two laborers.
- The 16×8 double barrel culvert crew included a foreman, a working foreman, two operators, two carpenters, and four laborers.
- The bridge crew was made up of a foreman, a crane operator, one carpenter, and three laborers.
What services did you provide for Design/Build, planning, engineering, site preparation, safety planning before the project could being work?
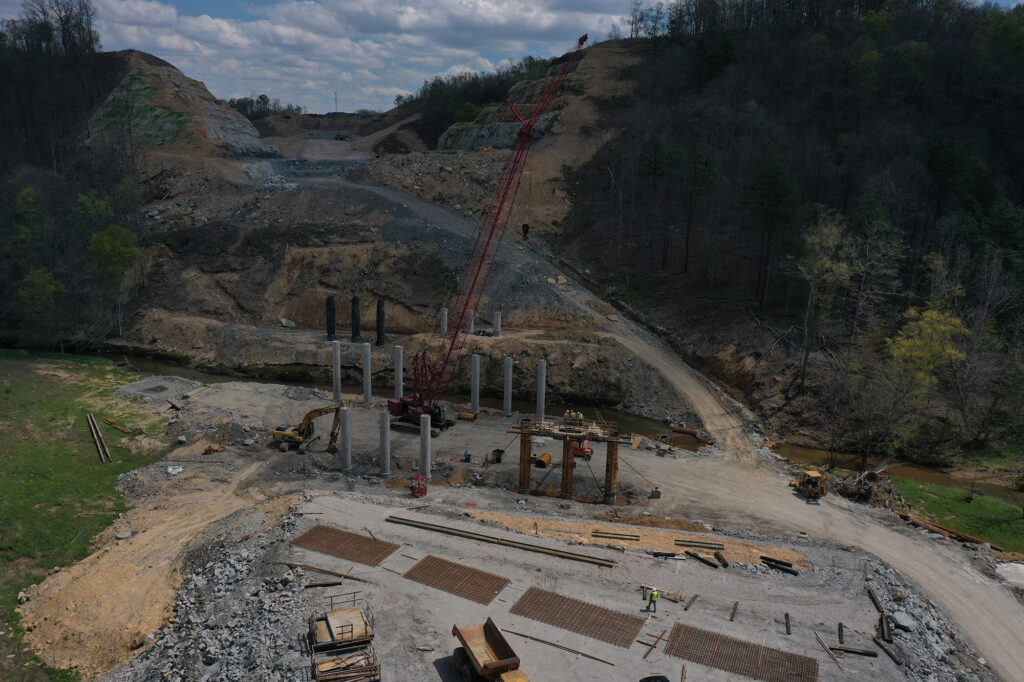
Before beginning work on the project, we provided a range of essential services in Design/Build planning, engineering, site preparation, and safety planning. Our initial focus was on collaborating with Hi-View LLC to determine where to begin construction, ultimately deciding to start with the Reinforced Concrete Box Culvert (RCBC) 4×6 box culverts. Completing the culverts first allowed Hi-View, the prime contractor, to begin moving materials into the cuts and fill areas afterward. Site preparation involved close coordination with Hi-View to ensure safe access and adequate working space for all construction activities.
Safety was a top priority in each structure, and specific measures were implemented for different components. For the culverts, we ensured safe access and egress by sloping the soil during excavations. We also installed proper walkways with handrails on top of the culvert formwork when working above six feet off the ground. For bridge construction, we established similar safety precautions, including walkways and handrails on both the formwork and bridge overhang during superstructure construction. Additionally, we provided lifelines on top of pier caps and beams, along with fall protection harnesses and lanyards, to ensure worker safety throughout the project.
What challenges or issues had to be remedied before construction could begin and during construction?
With a job of this size there were many issues and concerns that needed to addressed and resolved before we could begin the job. Here are a few that were resolved:
- Site Planning: HBC coordinated with the prime contractor to establish site access during the planning stages, allowing for initial site preparation at the proposed locations for culverts and bridges prior to mobilization. Many of these structures required creek crossings or even a roadway cut through the mountains to enable the start of construction work.
- Material Logistics: While the job was in progress, a global pandemic occurred, leading to delays in sourcing materials. Although these delays did not significantly impact HBC’s overall timeline for the project, we occasionally faced wait times for various products to be fabricated and shipped.
- Various Plan Dimensions Errors: When these issues were identified, Haydon Bridge submitted a Request for Information (RFI) to the Kentucky Transportation Cabinet (KYTC). The KYTC would then collaborate with the designers to source solutions and resolve the discrepancies.
- Foundation Issues at Double Barrel Culvert, during the site preparation, HI-View found unsuitable soils for the foundation of the culvert. While working with the KYTC, it was determined to undermine the soil to solid rock and replace place granular embankment. Thus, resulting having to also redesign the culvert with additional reinforcement to make it a “Non- Yeilding Foundation”.
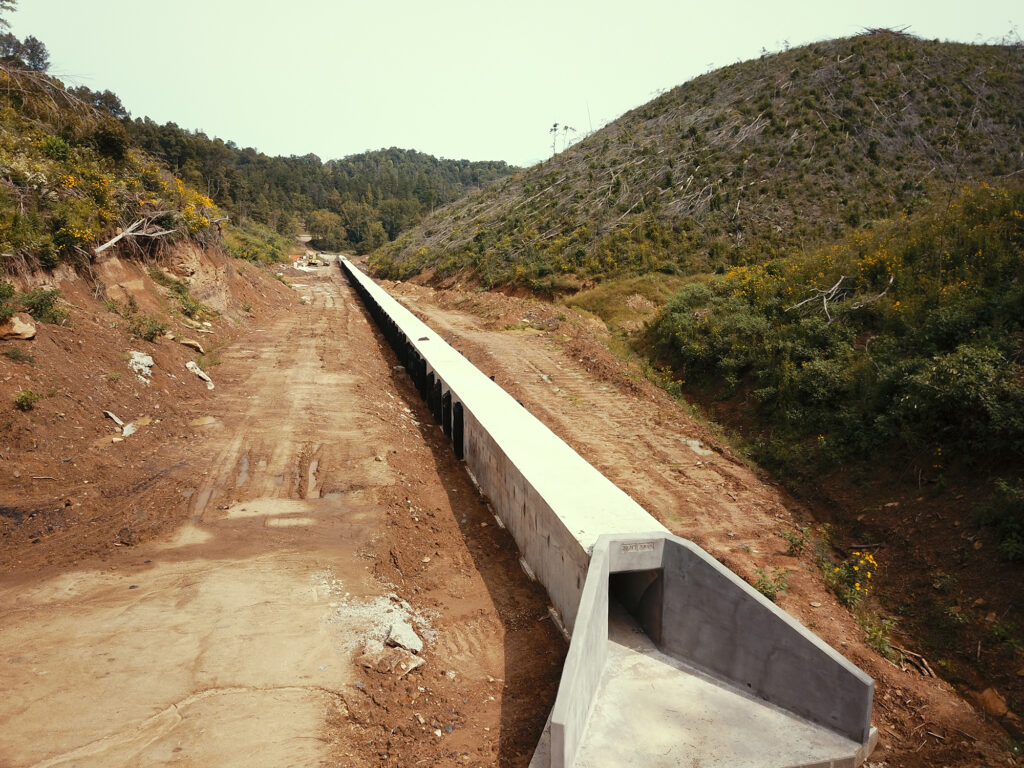
What were the steps for each phase of the project?
PHASE 1: Constructing 4×6 Box Culverts:
- Begin with excavation and grading the foundation for the culvert footer.
- Form the footer, then install the reinforcement and pour the concrete.
- Once the footer is set, remove the forms and install wall reinforcement.
- Form and pour the walls next.
- Dismantle the inside wall forms and install the “stay-in-place” forms.
- Finally, install reinforcement and pour the top slab.
- The process for each 4×6 culvert followed these same steps.
PHASE II: Constructing the Johnson Creek Twin Bridges:
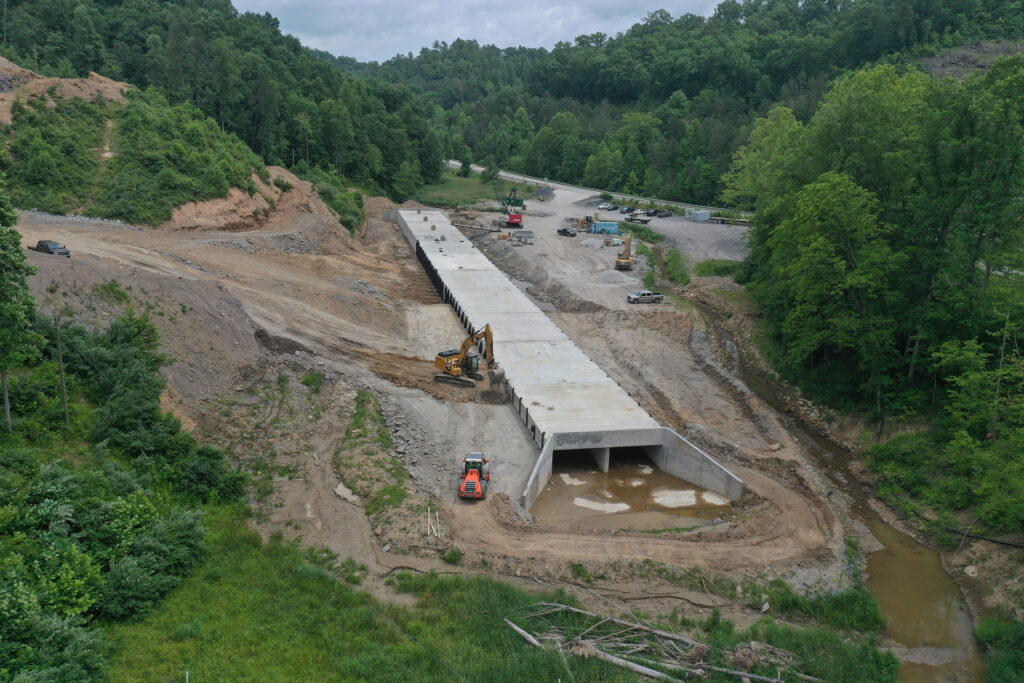
- Begin with rock sounding and coring to assess the true location and quality of the rock, finalizing the drilled shaft tip elevations.
- Install the drilled shafts.
- Construct the columns, web walls, and caps at the pier.
- Drive the piling at the end bents.
- Build the end bent cap to complete the substructure construction.
- Set the beams in place.
- Install the “stay-in-place” forms, then form and pour the deck.
- Complete the superstructure by pouring the barrier walls, dismantling the forms, and finishing the walls.
- Finally, apply masonry coating to the faces of the walls to finish the twin bridges.
- For the Johnson Creek project, we were able to complete both bridges simultaneously.
PHASE III: Constructing the Double Barrel Box Culvert:
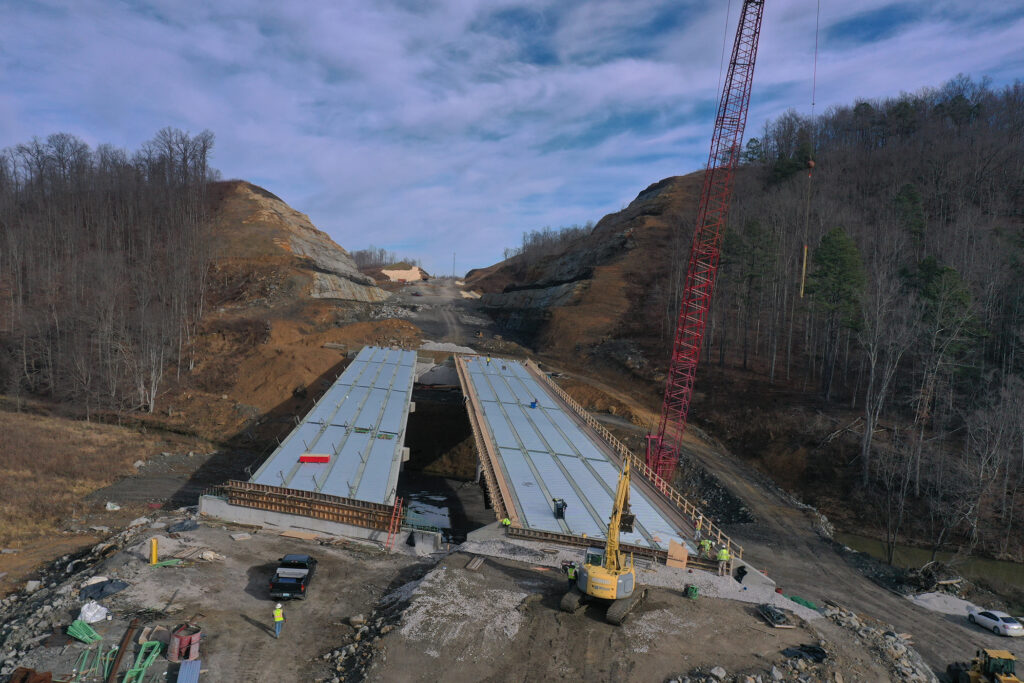
- The start of the double barrel box culvert construction faced delays due to unfavorable subgrade conditions, necessitating a redesign to incorporate a “Non-Yielding Foundation.” This involved undercutting the poor soils down to solid rock and installing crushed rock to create a stable subgrade. Hi-View was responsible for preparing the site prior to our mobilization for construction.
- Once the site was prepared, we began constructing the footer, completing most of it first. The footer pours needed to be strategically timed with the concrete plant due to the large quantities required. Each 50-foot section poured consisted of approximately 250 cubic yards of concrete.
- Next, we focused on the inlet walls and wings, pouring 60-foot sections for each wall.
- Finally, we completed the top slab, pouring it in 50-foot sections, similar to the footer but in larger quantities. The top slab was crucial in the sequence of the culvert construction due to the concrete strength requirements that needed to be met before we could remove the falsework and advance to the next section. Typically, this process took about one week to complete before proceeding to the next top slab.
PHASE IV: Constructing the Cutino Road Twin Bridges:
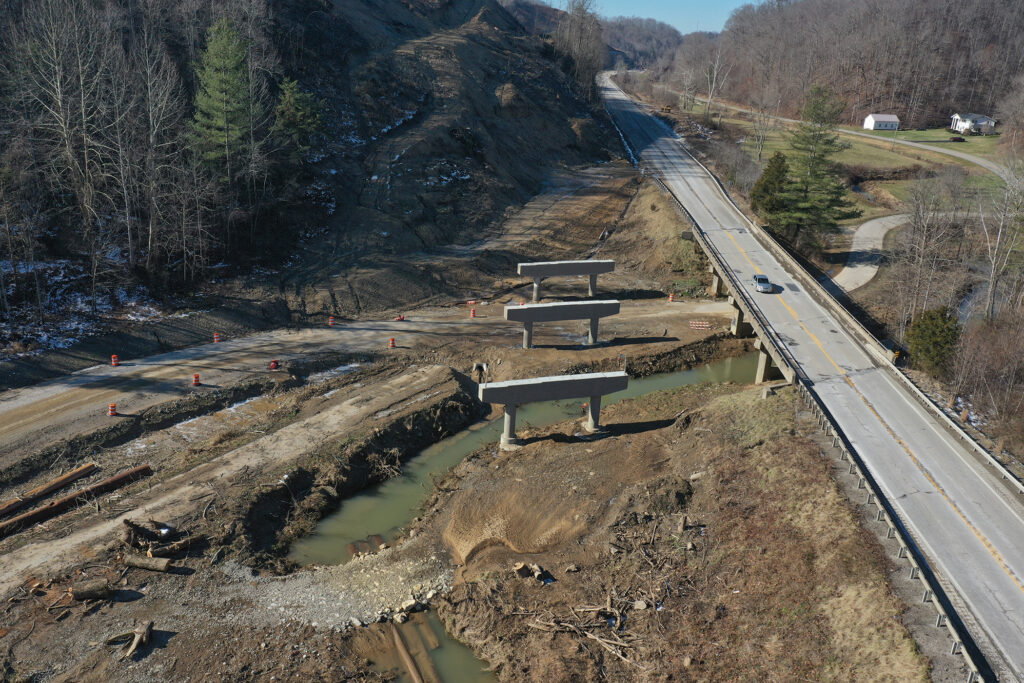
- The construction process for the Cutino Road bridges closely mirrored that of the Johnson Creek project. It began with rock sounding and coring to assess the true location and quality of the rock, finalizing the drilled shaft tip elevations.
- Next, we installed the drilled shafts, followed by building the columns and caps at the pier.
- We then set the piling at the end bents and constructed the end bent cap to complete the substructure.
- Afterward, the beams were set in place, and we installed the stay-in-place forms before forming and pouring the deck.
- The superstructure was completed by pouring the barrier walls and finishing the walls after removing the forms.
- Finally, we applied masonry coating to the faces of the walls to finish the set of twin bridges.
For the Cutino Road project, we completed the substructure for the eastbound bridge first but then had to wait six months for the embankment to be installed before finishing the structure. Once the eastbound bridge was complete, a traffic switch occurred, allowing for the demolition of the existing bridge and the construction of the westbound bridge.
PHASE V: Constructing the Cow Creek Twin Bridges:
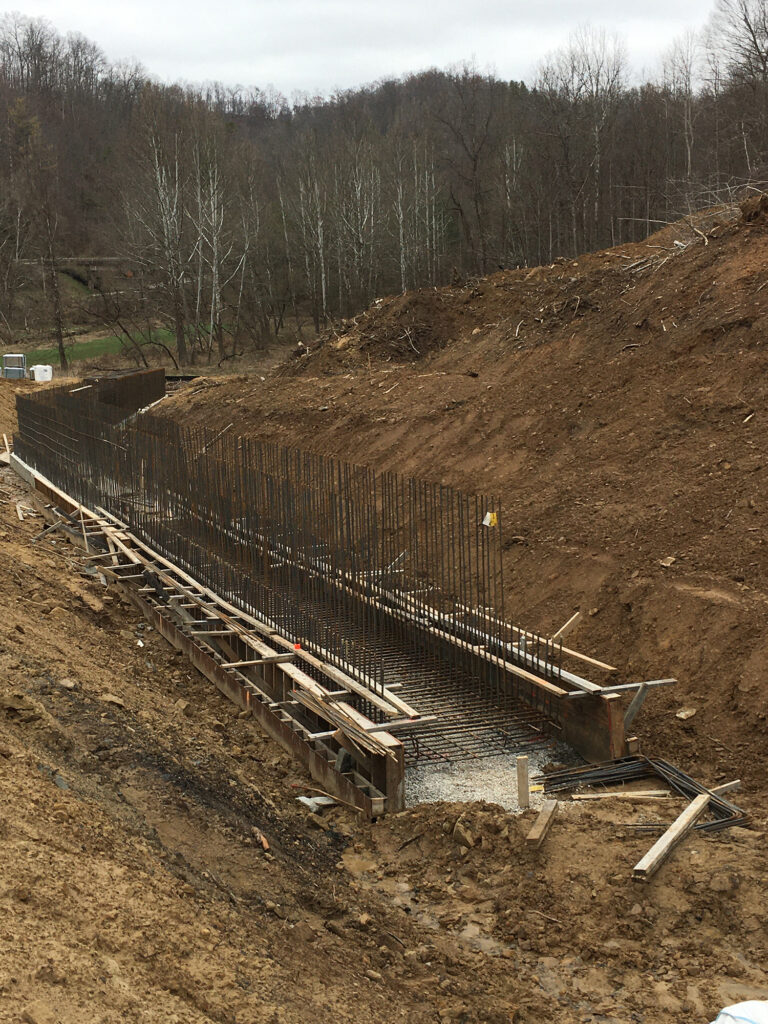
- Initially, we successfully constructed three of the four piers for both twin bridges. However, construction was delayed due to traffic phasing issues and a conflict with Pier 2 on the westbound side, which was located directly above an existing box culvert that needed to be demolished before work could proceed.
- After resolving the phasing issues and switching traffic, we were able to complete the construction of the final pier.
- Once the piers were finished, Hi-View installed the embankments for both end bents.
- Next, we constructed the end bents and set the beams in place.
- We then installed the stay-in-place forms and proceeded to form and pour the deck.
- The superstructure was completed by pouring the barrier walls and finishing the walls after removing the forms.
- Finally, we applied masonry coating to the faces of the walls to complete the set of twin bridges.
PHASE VI: Final Box Culvert 8×6:
- As with the other culverts, Hi-View facilitated the initial site preparations, after which we proceeded with footer construction, followed by the completion of the walls, wings, and top slab.
- Construction commenced shortly after the Cow Creek project was underway. Once traffic was switched from the existing parkway route to the temporary alignment, we were able to begin work on the culvert.
How well did you communicate the progress of the project to the owner and related parties?
We maintained effective communication regarding the project’s progress with the owner and related parties through various methods. Day-to-day interactions with onsite inspectors ensured that each task was addressed promptly and efficiently. Additionally, we held monthly progress meetings with the contractors and Kentucky Transportation Cabinet (KYTC) members to discuss the overall status of the project. These meetings provided an opportunity to review the previous month’s progress and outline projected upcoming events, fostering transparency and collaboration among all stakeholders.
What were the outstanding features of this project, and why are you proud of its final completion?
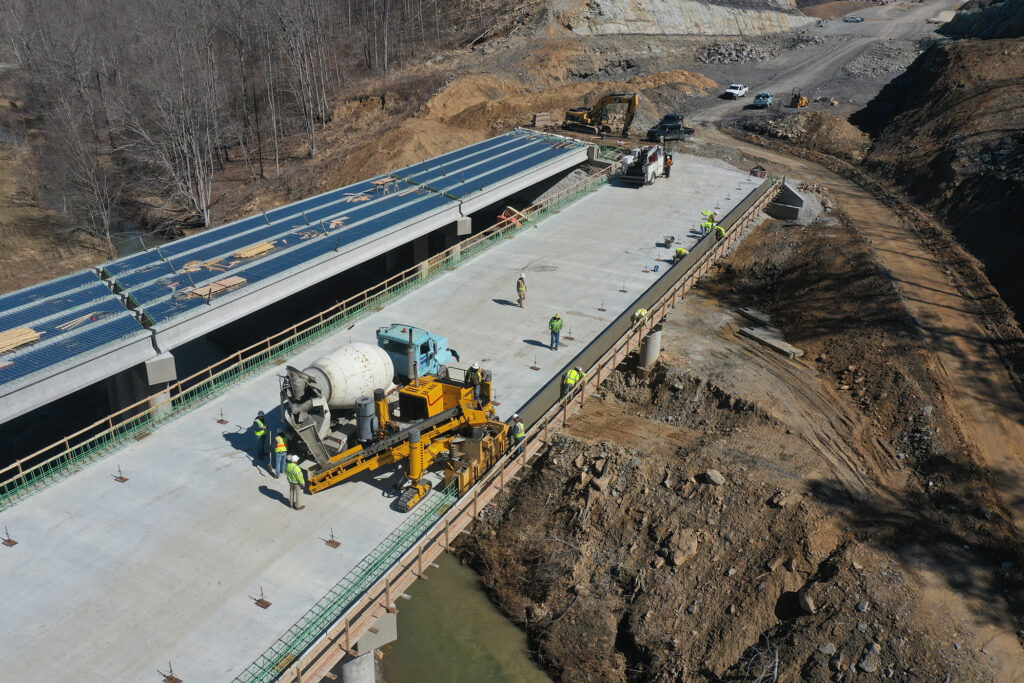
The Magoffin County section of the Mountain Parkway Expansion showcases several remarkable features, particularly in bridge and culvert construction:
- Innovative Bridge Design: The bridges in this section employ advanced engineering techniques, ensuring durability and resilience. They utilize modern materials and construction methods to withstand heavy traffic and environmental stresses.
- Enhanced Safety Features: Prioritizing safety, the project includes wider lanes, improved guardrails, and better visibility, all contributing to a safer driving experience for all users.
- Efficient Water Management: The reinforced concrete box culverts are engineered to manage significant water flow, mitigating the risk of flooding and erosion. This design ensures the longevity of the roadway and surrounding infrastructure.
- Environmental Considerations: The construction process incorporates measures to minimize environmental impact, such as erosion control and habitat preservation. These efforts help protect the local ecosystem while delivering essential infrastructure improvements.
- Aesthetic Integration: The design of the bridges and culverts is harmonized with the natural landscape, blending seamlessly into the environment. This consideration not only enhances visual appeal but also preserves the area’s natural beauty.
Collectively, these features contribute to a robust, safe, and environmentally friendly infrastructure that will serve the community for years to come, making us proud of the project’s final completion.
How will this project’s construction contribute to the community by providing safe and durable transportation roadways and bridges?
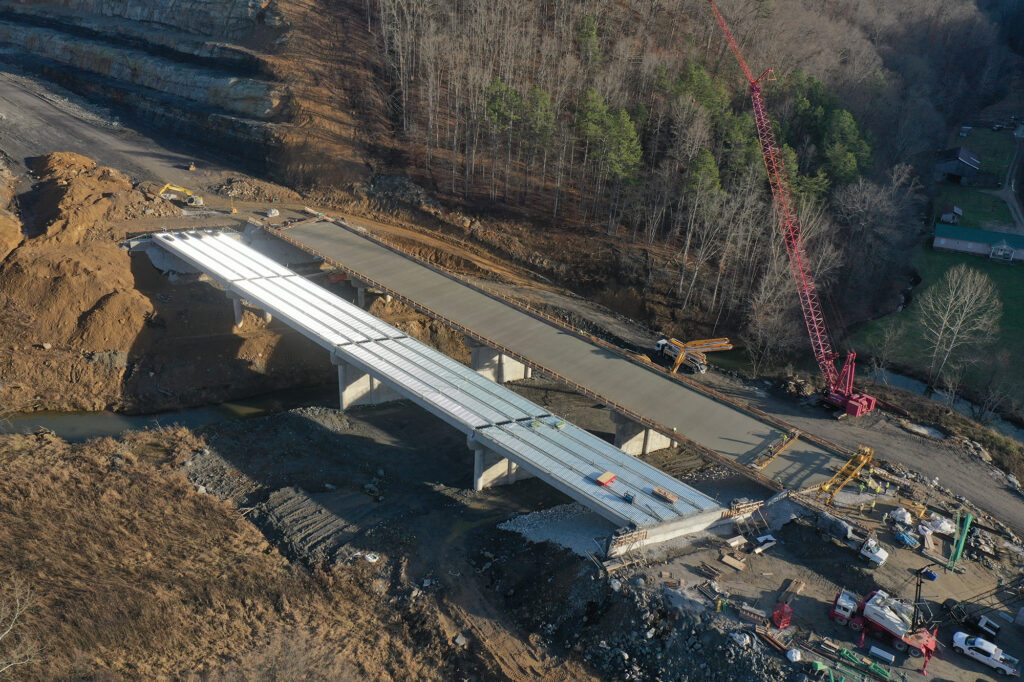
- Improved Safety: The new bridges and widened roadways incorporate modern safety features, including wider lanes, enhanced guardrails, and improved visibility. These upgrades significantly reduce the risk of accidents, ensuring a safer driving experience for all users.
- Durability and Longevity: The project utilizes advanced construction materials and techniques that guarantee the new infrastructure will be durable and require less maintenance over time. This translates to fewer disruptions and a more reliable transportation network.
- Economic Growth: By enhancing connectivity, the project supports local businesses and attracts new investments to the region. This improved infrastructure can lead to job creation and stimulate overall economic development.
- Environmental Considerations: The project incorporates measures to effectively manage water flow and reduce flooding, which safeguards both the infrastructure and the surrounding environment. These efforts are essential for maintaining the area’s natural beauty and ecological balance.
Why choose Haydon Bridge Company for your future projects?
Since 1972, Haydon Bridge Company’s mission is to deliver safe, cost-effective projects on schedule, exceeding quality standards while maintaining a professional relationship with clients based on our core values. Using our core values as the foundation, we will deliver safe, cost-effective projects on schedule, while exceeding quality standards and maintaining a professional relationship with clients. Our company provides our employees with a safe, honest and team-oriented work environment, where individuals are allowed to grow while working with a team to provide exceptional workmanship within the heavy civil construction market.