Our mission statement includes safety as a priority, and it’s the focus of every project we complete and every contract we are awarded. While some may view safety as the necessary evil, at Haydon Bridge, we view it as a worthy investment in our people that is critical to our continued business success & growth. The employee that is trained in safe work practices is not only more productive in the long run but they are less likely to be injured and will lead a healthier life down the road. We believe this is a smart investment in our future.
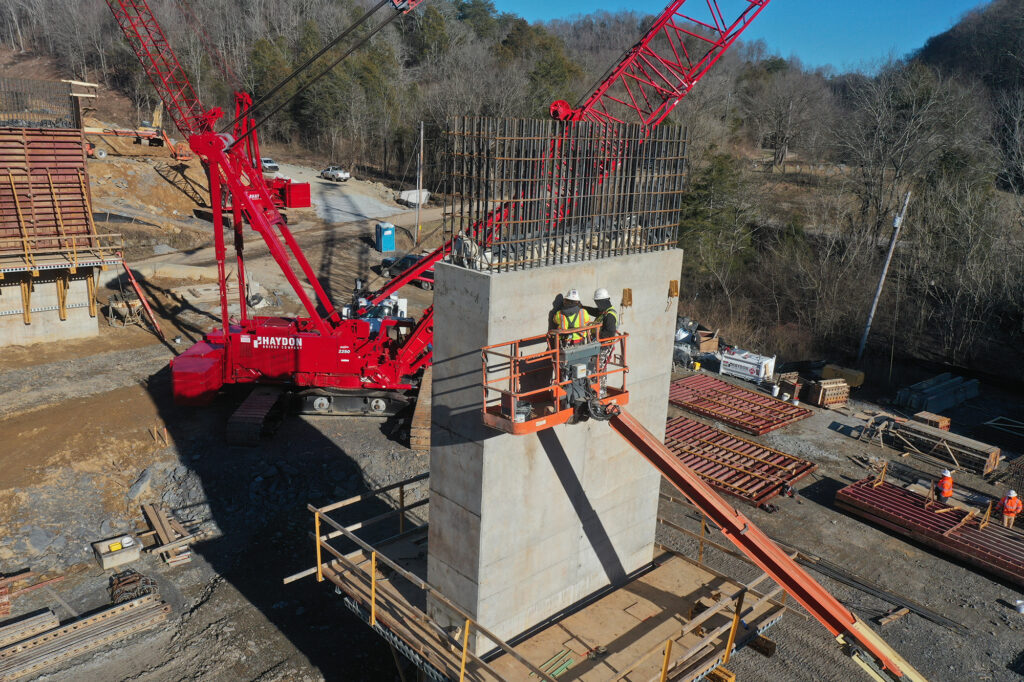
In these Safety Blogs, we’ll introduce you to some of the investments we make in time, training or equipment to keep our crews safe. At a high level, employee safety can be broken down into 3 segments: Equipment, Training and Inspections.
Safety Equipment:
From sub-structure work below grade (ie. Bridge footers) to super-structure work in the air (ie. bridge beams and bridge deck), Haydon Bridge must consider all facets of the scheduled scope of work when it comes to employee safety. Work processes must be planned, OSHA regulations must be understood and safety equipment must be available when needed.
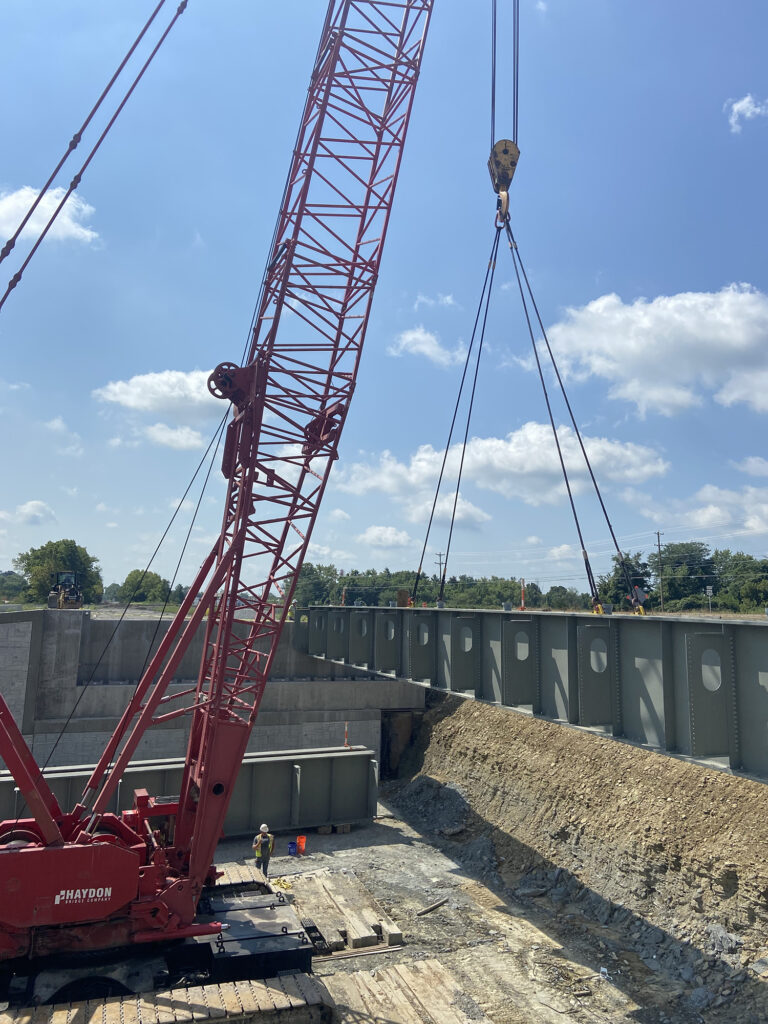
Everyone from the Project Manager to the front-line Laborer must be on the same page and understand the work process, how to use the safety equipment and how to complete them safely. Delays due to missing equipment/materials can be costly but are minimal when weighed against the potential risk to employee injury or death.
In an effort to minimize delays to work, Haydon Bridge owns most of the common safety systems used to protect workers. Trench boxes, sheet piling, cofferdams are systems designed to keep our crews safe when working in constricted excavations. Respiratory protection equipment and trained work practices keep our crews healthy when working with concrete dust that likely contains silica. Passive fall protection systems like guardrails or active fall arrest systems including anchors, lifelines and harnesses are constructed or used, respectively, when working at height. And finally, basic Personal Protective Equipment is used daily when on the job.
Add it up, and Haydon Bridge has invested and continues to invest significant resources to the equipment and PPE that keep our employees safe on the job.
Safety Training:
Haydon Bridge believes so strongly in safety that we employee a full-time Safety Director, Bill Pettus. Bill’s duties include:
- identifying opportunities to minimize workplace injuries, accidents, and health problems
- leading jobsite employee training on applicable OSHA safety standards and company policies
- reviewing safety training and recommends revisions, improvements, and updates
- conducting safety inspections and audits to assess employee compliance with safety regulations
- working with field employees in a hands-on manor to identify process safety gaps and to help employees understand safe working practices
- Developing annual offsite leadership training & development
The investment in a full-time Safety Director is something many companies our size may not make. We firmly believe that our employees are our most valuable asset and we must ensure that they are afforded training and work environment they deserve.
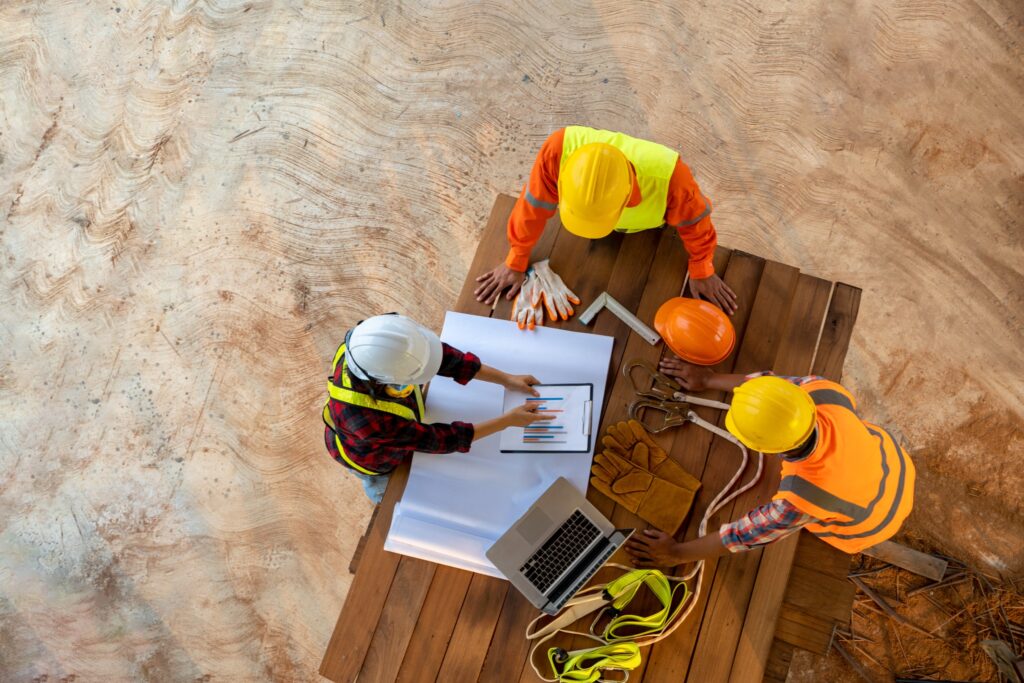
OSHA requires that all employees be trained to identify workplace hazards, how to mitigate the hazard or protect themselves from it and re-trained when workplace conditions or hazard limits change. Over the past 10-years, we have developed a robust safety program that includes various topics, all relative to our jobsite safety. Employees are trained on these topics in jobsite talks or during offsite winter training sessions per OSHA expectations. Our Safety Manual is broken down into more than a 100+ documents based on topics, including:
- Fire Safety
- Work Zone Traffic Control
- Signaling Safety
- Ladder Safety
- Rigging Safety
- Respiratory Protection
- Electrical Safety
- Crane Safety
- Power Tools Safety
- Aerial Lifts Safety
- Fall Protection
Inspecting what we Expect:
Even when proper equipment is used and employees know how to use it, we can still have instances where three are missteps, or literal steps are missed (pun intended). For this reason, we implement safety inspection into our process. Foremen are expected to complete and have their compensation closely connected with monthly jobsite inspections. Our Safety Director completes multiple jobsite inspections each month on each job. Project Managers and Owners all review daily foreman reports to ensure production goals are being maintained and safety procedures are followed. In short, we spend significant amounts of time immersing ourselves into the ‘inspections’ of our jobsites.
Additionally, we welcome 3rd party inspections of our jobsites. We believe in open and transparent jobsite inspections. Afterall, if done correctly, there is nothing to hide, right? For this reason we welcome the Kentucky Occupational Safety & Health (KOSH) Training and Education division, our workers comp insurance carriers and other insurance related inspectors to our jobsites and proactively ask for reviews of our safety programs and processes.
Conclusion:
Haydon Bridge takes jobsite and employee safety very seriously! We believe in employee education, transparency and providing our workers with the tools and materials to do the job right the first time and safely every time. A properly trained & empowered workforce is critical to a safe working environment. Time and money devoted to equipment, training and jobsite inspections is not an expense, it’s an investment in our employees. It’s not just the smart thing to do, it’s also the RIGHT thing to do!